Choosing the Right Gas for Your Welding Needs
Understanding the Importance of Gas in Welding
Welding is a process that joins materials, usually metals or thermoplastics, by causing coalescence. The choice of gas plays a crucial role in determining the quality and characteristics of the weld. Selecting the right gas not only affects the strength and appearance of the weld but also impacts safety, cost, and productivity.
The primary function of shielding gases is to protect the weld from atmospheric contamination. However, different welding processes and materials require specific types of gases to achieve optimal results. Understanding the properties and applications of different gases can help you make an informed decision.
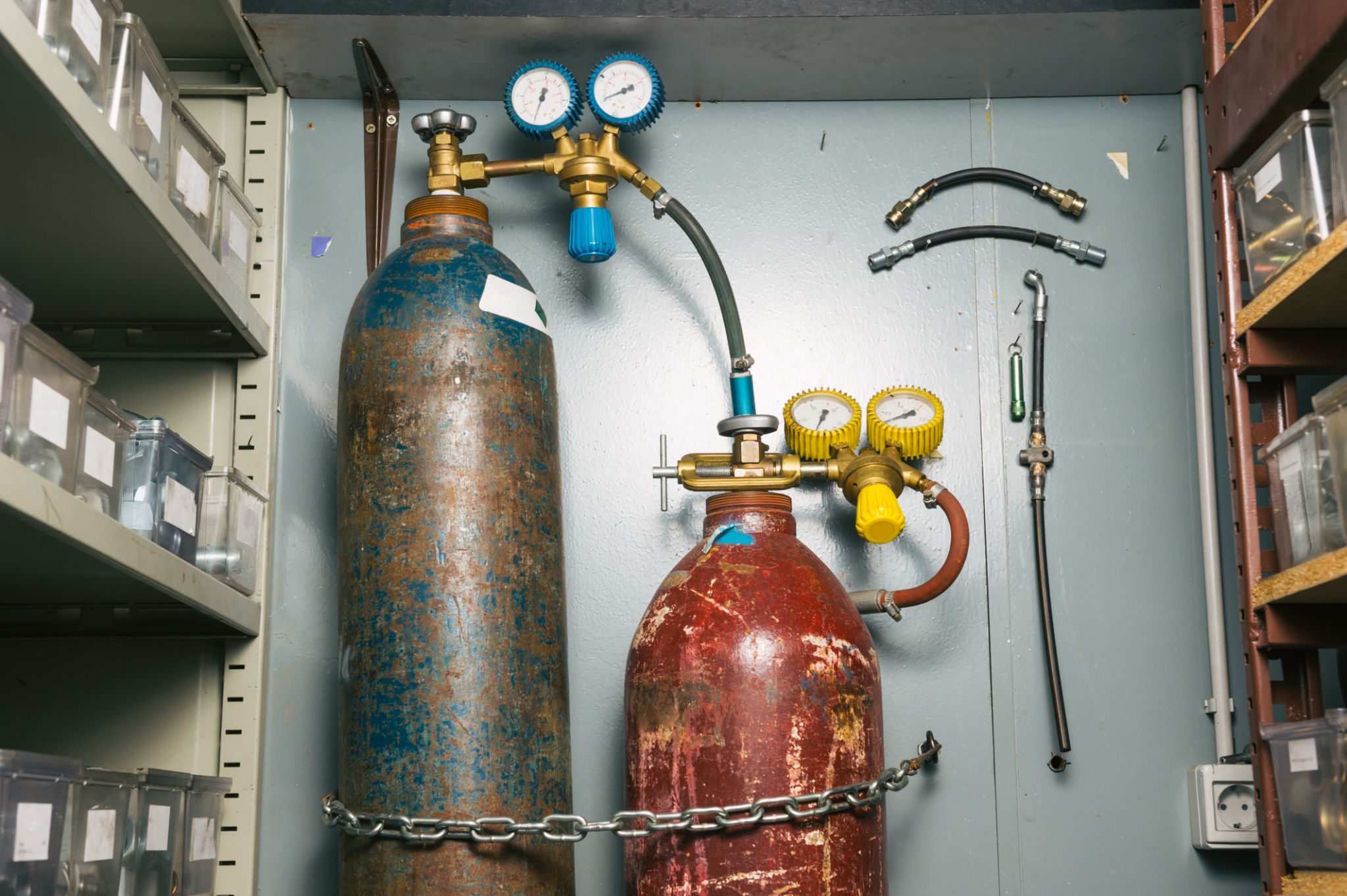
Common Types of Welding Gases
There are several types of gases used in welding, each with unique properties and applications. Some of the most common gases include:
- Argon: Often used for TIG and MIG welding, argon provides excellent protection against oxidation and is known for producing clean and smooth welds.
- Carbon Dioxide: Widely used in MIG welding, carbon dioxide is cost-effective and provides deep penetration for thicker materials. However, it can lead to more spatter compared to argon.
- Helium: Typically used in combination with other gases, helium allows for faster welding speeds and deeper penetration, making it ideal for thicker materials.
Choosing the Right Gas for Your Welding Process
The choice of gas largely depends on the welding process being used. For instance, in TIG welding, pure argon is often preferred due to its ability to provide a stable arc and high-quality welds. On the other hand, MIG welding can utilize a variety of gas mixtures to achieve different effects.
When working with stainless steel or aluminum, a mixture of argon and helium can provide better heat management and improve weld quality. Each combination has its benefits, so understanding your specific needs is essential.
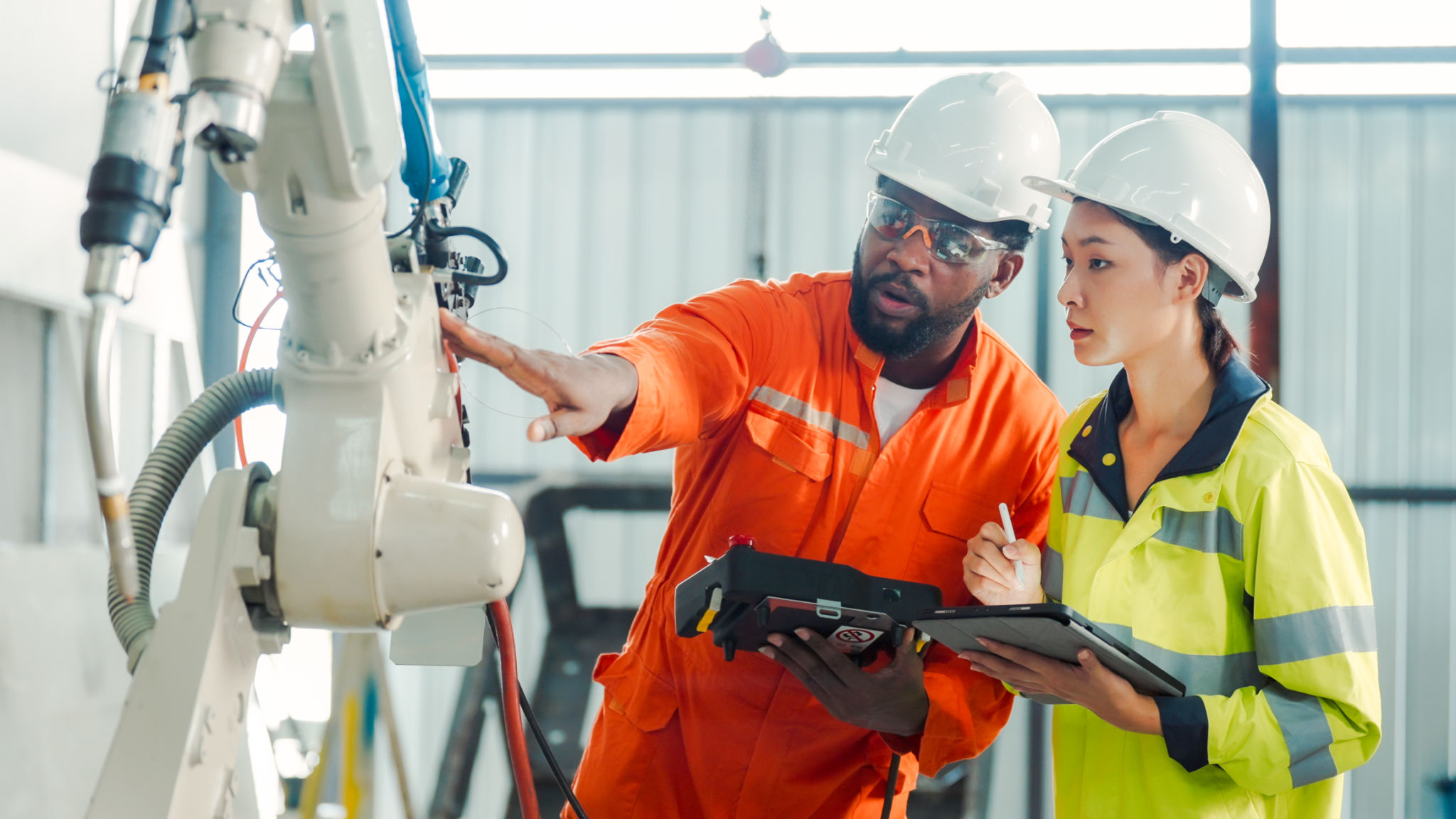
Considering Material Type and Thickness
The type and thickness of the material being welded are important factors in selecting the appropriate gas. For instance, thicker materials may require a gas that provides deeper penetration, such as a mix of argon and carbon dioxide. Conversely, thinner materials may benefit from pure argon to prevent burn-through.
Additionally, different metals react differently to certain gases, so it’s important to consider the material's properties when making your choice. Consulting with a welding expert can provide valuable insights into the best gas options for your specific application.
Cost and Availability
While performance is a key factor, cost and availability also play significant roles in choosing the right gas. Some gases are more expensive but offer superior performance for specific applications. It’s important to balance cost-effectiveness with the quality requirements of your project.

Additionally, ensure that your preferred gas type is readily available from local suppliers to avoid delays and disruptions in your welding operations. Establishing a good relationship with your supplier can also provide access to expert advice and support.
Safety Considerations
Safety should always be a priority when working with welding gases. Ensure that you are familiar with the safety guidelines for handling and storing each type of gas. Proper ventilation is crucial to prevent the buildup of harmful fumes and gases during the welding process.
Using appropriate protective gear such as gloves, goggles, and masks is essential to protect yourself from potential hazards. Staying informed about safety practices will help you maintain a safe working environment.
Conclusion
Choosing the right gas for your welding needs involves considering several factors such as the welding process, material type, cost, and safety. By understanding these elements, you can make informed decisions that enhance the quality and efficiency of your welding projects. Always consult with experts when in doubt and prioritize safety in every operation.