Comprehensive Guide to Using Argon Gas in Welding
Introduction to Argon Gas in Welding
Argon gas plays a crucial role in the welding industry, providing a protective atmosphere that ensures high-quality welds. This inert gas is often used in various welding processes, including TIG (Tungsten Inert Gas) and MIG (Metal Inert Gas) welding. Understanding how to effectively use argon gas can significantly enhance your welding projects, ensuring precision and strength in your final product.
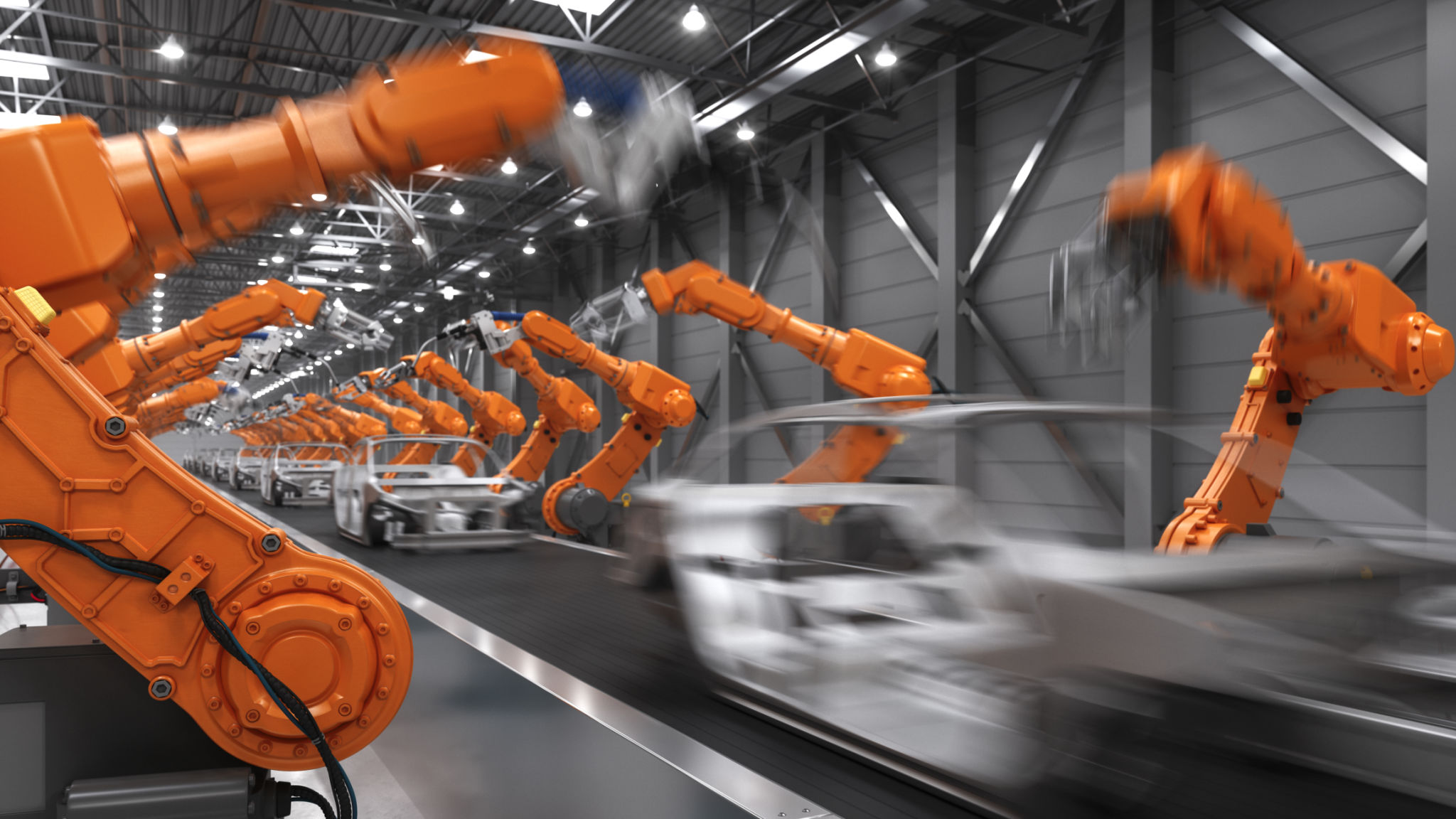
Why Use Argon Gas?
The primary reason for using argon gas in welding is its inert nature, which prevents oxidation and contamination of the weld pool. This characteristic is especially important when working with reactive metals like aluminum and magnesium. Argon gas creates a stable arc and provides better arc control, allowing for smoother and cleaner welds.
Another advantage of argon is its ability to produce a narrow penetration profile. This benefit is particularly useful for thin materials, reducing the risk of burn-through and ensuring a neat finish. Additionally, argon is non-toxic and safe to use, making it a preferred choice for many welders.
Applications of Argon Gas
Argon gas is widely used in several welding processes, each benefiting from its unique properties. In TIG welding, argon is the most commonly used shielding gas due to its ability to maintain a consistent arc and produce high-quality welds with minimal spatter. It is also used in MIG welding, often in combination with other gases like carbon dioxide, to achieve different welding characteristics.

Beyond welding, argon gas finds applications in other industries such as metallurgy and electronics manufacturing. Its ability to create an inert atmosphere makes it ideal for processes that require a high degree of purity and precision.
How to Use Argon Gas Effectively
To use argon gas effectively in welding, it is essential to understand the correct flow rate for your specific application. The flow rate can influence the quality of the weld, so adjusting it according to the material thickness and type is crucial. Generally, a flow rate between 15-25 cubic feet per hour (CFH) is recommended for most welding tasks.
Proper equipment maintenance is also vital when working with argon gas. Regularly check hoses, regulators, and connections for leaks or damages. Ensuring that your equipment is in good working condition helps maintain consistent gas flow and prevents contamination.
Safety Precautions
While argon gas is non-toxic, it can displace oxygen in confined spaces, posing a risk of asphyxiation. It is important to ensure adequate ventilation when using argon gas in enclosed areas. Always use appropriate personal protective equipment (PPE) such as gloves, helmets, and protective clothing to safeguard against potential hazards during the welding process.
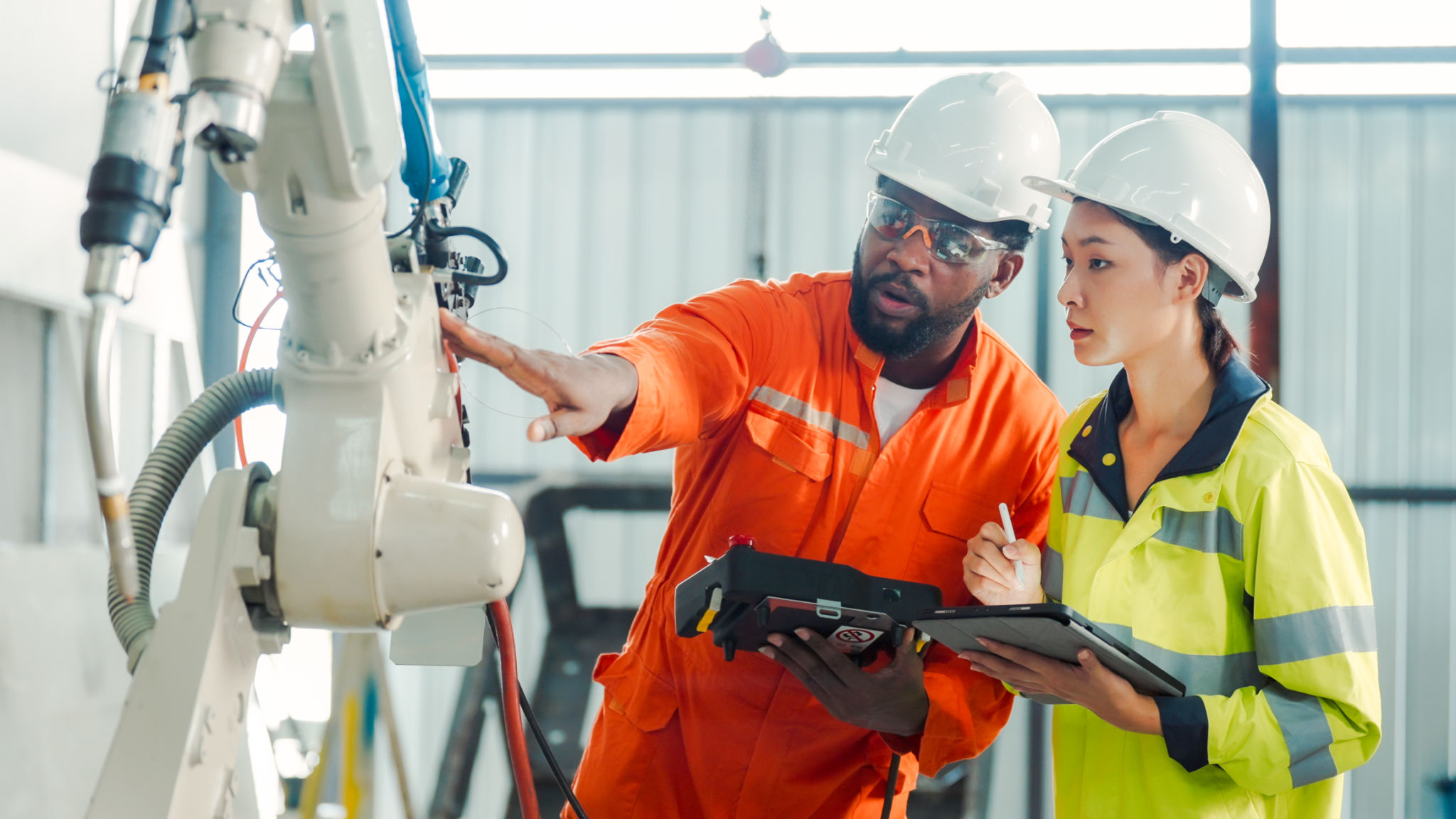
Furthermore, familiarize yourself with emergency procedures and have safety equipment like fire extinguishers readily available in your workspace. Following these safety precautions will help prevent accidents and ensure a safe working environment.
Conclusion
Argon gas is an invaluable resource in the world of welding, offering numerous benefits that enhance both the quality and safety of welds. By understanding its applications and adhering to best practices for usage and safety, welders can achieve superior results in their projects. Whether you're a seasoned professional or a beginner, mastering the use of argon gas can greatly improve your welding capabilities.